Fire and Explosion
BlazeTech has developed a number of fire and explosion models over the years and performed specialized testing to validate the modles, including the development of specialized test rigs:
- Hot surface ignition test rig and model to determine the lowest surface temperature that would ignite a leaking fluid
- Pool Fire to predict the dimensions, duration, temperature and rate of heat transfer from a pool fire
- Boiling Liquid Expanding Vapor Explosion or BLEVE to predict the overpressure and failure of a tank containing liquid due to external heat (for example, from a pool fire)
- Deflagration of a fuel-air mixture in a container (BlazeTank)
- Dust Explosions for explosion of micro and nanoparticles dispersed into air and ignited using a strong ignition source
- Vapor Cloud Fire
- Flash Fire
- Jet Fire
- Unconfined Vapor Cloud Explosions
- LNG Pool and Vapor Fires
- Oil Well Fires
- Ignition Sources
- Petrochemical Fires and Explosions
Also, the above modules can be coupled together to model domino effects.
Hot Surface Ignition Test Rig and Model
Over the years, BlazeTech tested and modeled the hot surface ignition temperature of various flammable liquids in bench scale tests and large-scale simulated aircraft engine nacelles. While the subject has been investigated by others, none have addressed the case of heated high temperature fuels or have the unique features of our test rig. Our configurable test rig has the capability to handle different simulated aircraft geometries (flat/curved surfaces) at various orientations, degrees of confinement and airflows to produce natural or forced convection; a thermal design of the hot surface that maintains the temperature constant during the test despite the quenching effect of liquid which has resulted in an inaccurate measure of ignition temperature by others; and a de-oxygenator to reduce the dissolved oxygen content in the fuel down to 1 ppm to prevent coking at high temperature. The rig is also equipped with a micro annular gear pump that can precisely deliver fluids on the order of microliters per second, and a high-powered heating system able to maintain surface temperatures in excess of 1000 °F. Thus, it provides excellent control of the hot plate temperature, the fluid flowrate, temperature and pressure, and the airflow conditions, all critical to get accurate data. The combustion products are safely exhausted through the fume hood and variable-speed fan. The design was supported by our engineering models.
Design of the hot surface ignition apparatus.
Previous test surfaces on our rig include a 12" flat plate made of SiC, a 12" flat plate made of Inconel 718, a 4" outside diameter 1020 steel duct and a 4.5" outside diameter SiC duct. These hot surfaces and the injection conditions were designed to minimize plate quenching by liquid fuel injected at ambient temperature. With minimal quenching, the hot surface ignition temperature can be measured accurately and used to determine the kinetics of ignition. Using these kinetics, we developed a physicochemical model to predict what would happen for the case of larger fuel leaks that may produce quenching of the impacted hot surface. The minimum hot surface ignition temperature (MHSIT) depends on numerous test variables.
We have also translated the ignition results into ignition probability maps for Jet A.
Ignition probability (p) map for JP-8 interpolating between the measured data identified by points.
PoolFire
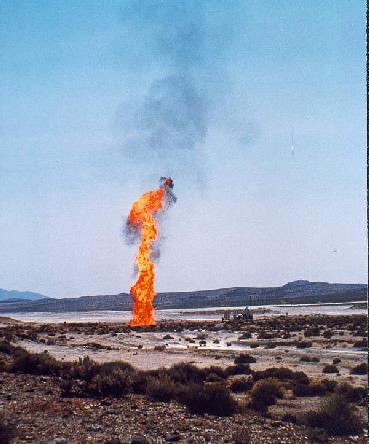
When a liquid phase fuel is released from a storage tank, it forms a pool on the ground. In the presence of an ignition source, this pool ignites and forms a pool fire. Heat is released from pool fires due to fuel combustion. A number of heat transfer processes are kicked off including heat transfer from ground to the liquid in the pool and radiation heat transfer from the fire to the pool. These processes are accounted in our PoolFire model.
PoolFire Model Inputs
- release parameters such as the type of release (continuous or instantaneous), amount/rate of fuel released and duration of release;
- properties of fuel such as molecular weight, density, boiling point, latent heat of vaporization, heat of combustion, heat capacity and burning rate (if available);
- properties of substrate on which the fuel is released such as surface roughness
- ambient conditions such as temperature, wind speed, atmospheric transmittivity
- dimensions, orientation and location of receptors with respect to the source for radiation heat transfer
PoolFire Outputs
- PoolFire dimensions as functions of time
- Various modes of heat transfer to receptors
BLEVE
Under rapid heating (for example, from a pool fire engulfing the tank), a tank containing pressurized liquid may fail suddenly producing an explosive effect. The liquid in the tank absorbs energy from the surrounding fire and heats up rapidly. The resulting increased rate of vaporization produced increases the ullage pressure. When this pressure exceeds a certain limit (characteristic of the material properties of the tank wall, wall thickness and temperature), the tank fails. The liquid released from the tank boils rapidly and expands. The resulting explosion may fragment the tank into pieces and propel them over large distances. If the hazmat is flammable, it may ignite and form a fireball posing additional hazard. This phenomenon is called a BLEVE or Boiling Liquid Expanding Vapor Explosion.
BLEVE accounts for the following key coupled processes:
- heat transfer:
- from flame to tank
- from tank walls to the liquid and vapor phases
- between liquid and vapor phases
- thermodynamic transformations within the tank and pressure buildup
- activation of pressure relief valve (or PRV) and venting
- wall stresses and material property degradation
- tank failure
- depressurization of liquid upon tank failure with concomitant thermodynamic transformations
Model Inputs
- tank geometry and tank wall thickness
- tank wall material properties such as density, heat capacity, temperature dependence of the yield strength
- properties of the hazmat such as molecular weight, density, heat capacity of liquid and vapor phases as functions of temperature, vapor pressure as a function of temperature
- vent conditions such as the settings on the Pressure Relief Valve (PRV) and the vent diameter
- characteristics of external source that initiates BLEVE (For example, if a fire initiate it, the dimensions of fire, flame temperature and the proximity of flame to the tank)
Model Outputs
- occurrence and time for tank failure
- venting rate and temperatures of various zones in the tank as functions of time
- occurrence of a BLEVE
- Blast strength associated with BLEVE
- Blast strength at various receptor locations
Unconfined Vapor Cloud Explosions
We compiled the TNT yields reported for major historical explosions involving accidentally-released fuels. To interpret the large scatter in the data, we delineated two factors: the fraction of chemical energy released in the explosion and the fraction of released energy transmitted to the blast. The latter factor varied little and placed a theoretical upper limit on yield (consistent with the data). The former was very accident-specific and explained the data scatter.
LNG Pool and Vapor Fires
For the Coast Guard, we participated in the design of large spill tests of liquefied natural gas fires (10,000 gallons). Both pool and vapor cloud fires were produced. We calculated the flame emissive power based on measurements of flame shapes, sizes and spectral and total radiation fields. Also, we identified and interpreted new, salient features of the dynamics of vapor cloud fires. This study formed the basis of state-of-the-art fire models in these areas, which we have tailored and applied to a variety of fuels.
Oil Well Fires
For the Defense Threat Reduction Agency (DTRA), we have recently developed a model for the prediction of flame temperature, buoyancy flux and emissions from oil well fires.
Ignition Sources
For the Gas Research Institute, we conducted a survey of potential devices in a city that might ignite accidentally released vapor clouds of natural gas. Tests were conducted on the most likely devices such as cigarettes, traffic lights, automobiles, door-bell relays, street lights, etc. The results were converted into a probability of vapor cloud ignition.
Petrochemical Fires and Explosions
For several petrochemical plants, we modeled a variety of accident scenarios, including the venting of gases, spills of liquids, and two-phase flow releases. These releases may be followed by the formation of pool, trench or vapor cloud fires or by fireballs, BLEVEs, and explosions. In the case of fire, we calculated the thermal radiation field around the fire to estimate the hazard zones for burn injury or wood ignition. In the case of explosion, we calculated the pressure field around the explosion point to estimate the hazard zones using damage criteria for building collapse, ear drum rupture, window breakage, etc.